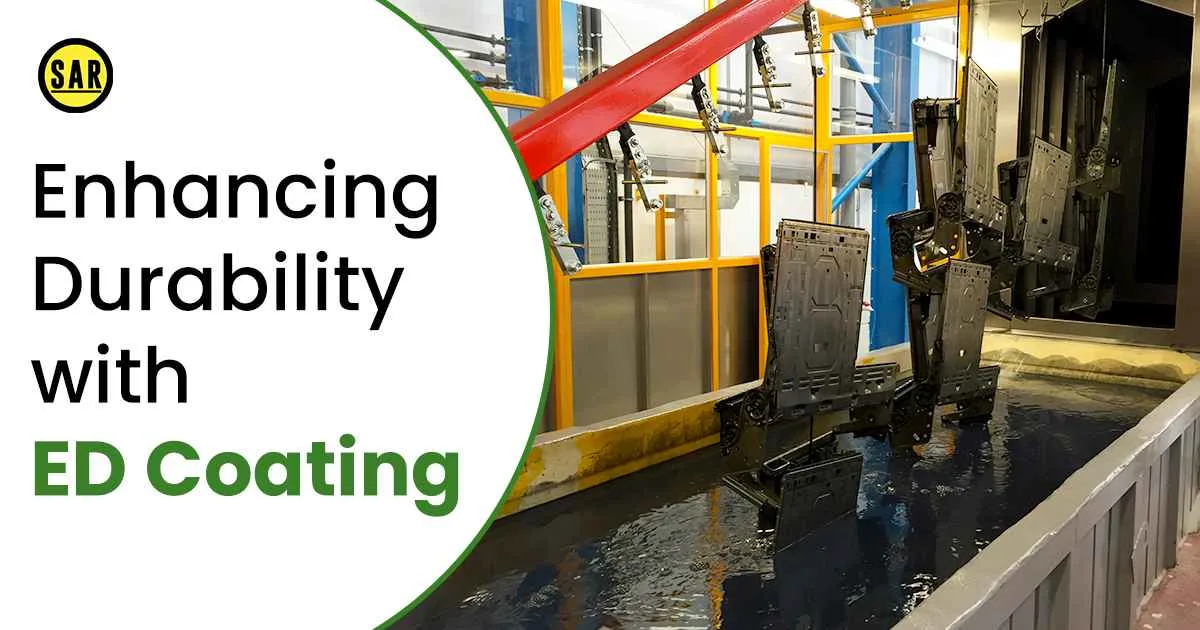
ENHANCING DURABILITY WITH ED COATING
Durability is a crucial aspect when it comes to various products and surfaces, especially those exposed to harsh environments or frequent use. To combat corrosion, abrasion, and other forms of damage, innovative coating technologies have been developed. One such coating that has gained significant attention is the ED coating (electron deposition) .
Electrode position coating, commonly known as ED coating, is a process that involves the application of a protective coating to various metal surfaces. It is widely used in industries such as automotive, aerospace, appliances, and construction. The coating provides excellent corrosion resistance, enhanced adhesion, and improved durability, making it a preferred choice for many manufacturers.
How Does ED Coating Work?
The process of electroplating begins with the preparation of the metal surface. The surface is thoroughly cleaned, ensuring the removal of any contaminants or oxides. It is then immersed in an electrolytic bath containing a mixture of water and the coating material. An electric current is applied, causing the coating material to deposit uniformly onto the metal surface. The thickness of the coating can be controlled by adjusting the voltage and duration of the process. Once the desired coating thickness is achieved, the part is rinsed and dried, completing the ED coating process.
Advantages of E-Coating
- Corrosion Resistance: It offers exceptional resistance to corrosion, protecting the underlying metal surface from rust and degradation caused by exposure to moisture, chemicals, and atmospheric elements.
- Adhesion: The electrodeposition process ensures strong adhesion between the coating and the metal substrate, minimizing the risk of delamination or peeling.
- Uniform Coating: Coating provides a uniform thickness across complex shapes and hard-to-reach areas, ensuring consistent protection throughout the entire surface.
- Enhanced Durability: With its superior resistance to abrasion, impact, and chemicals, ED coating significantly enhances the durability of the coated products, extending their lifespan.
- Environmentally Friendly: It is an environmentally friendly option as it produces minimal waste and has low volatile organic compound (VOC) emissions compared to traditional coating methods.
Applications of ED Coating
The versatility and effectiveness of ED coatings have led to their widespread adoption in various industries. Here are some notable applications:
- Automotive Industry: The coating is extensively used in the automotive industry to protect vehicle bodies, chassis, and components from corrosion, ensuring longevity and maintaining aesthetic appeal.
- Appliances and Electronics: Many appliances, such as refrigerators, washing machines, and dishwashers, incorporate ED to safeguard against moisture and chemical exposure, preventing rust and deterioration.
- Aerospace and Aviation: It finds applications in the aerospace industry, where it is utilized to protect aircraft components, structures, and fasteners from environmental factors, including moisture and salt spray.
- Building and Construction: Steel structures, window frames, and other metal components used in construction benefit from the corrosion resistance provided by ED coatings, extending their lifespan and reducing maintenance costs.
Enhancing Durability
The coating plays a pivotal role in enhancing the durability of various products and surfaces. Its protective properties ensure longevity, resistance to wear and tear, and reduced maintenance requirements. By applying an ED, manufacturers can improve the lifespan of their products and enhance their performance in demanding environments. Whether it's a car, an appliance, or a structural component, the application adds an extra layer of protection, ensuring that the item stands the test of time.
Protect, Preserve, and Prosper
The Ecoat is a highly effective solution for enhancing durability and protecting metal surfaces from corrosion, abrasion, and other forms of damage. Its uniform coating, strong adhesion, and excellent resistance to environmental factors make it an ideal choice for various industries. By incorporating E-coating into manufacturing processes, companies can produce long-lasting, reliable products that can withstand challenging conditions. With its numerous advantages and wide-ranging applications, It continues to contribute to the development of durable and robust products across different sectors.