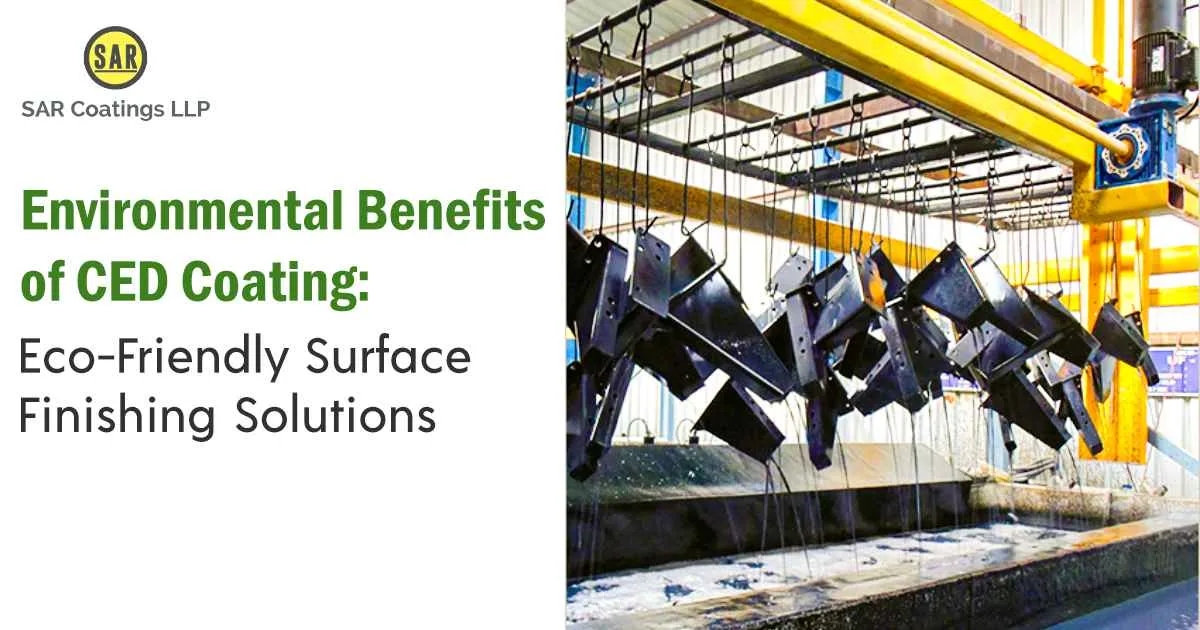
Environmental Benefits of CED Coating: Eco-Friendly Surface Finishing Solutions
CED (cathodic electrodeposition) coating, also known as electrophoretic coating or electrocoating, provides several environmental benefits as an eco-friendly surface finishing solution. These benefits contribute to sustainable practices and reduced environmental impact. Coating processes use water-based formulations, significantly reducing or eliminating the need for volatile organic compounds, which are chemicals that evaporate at room temperature and contribute to air pollution, smog formation, and potential health risks. It is a process used for surface finishing that involves the deposition of a protective coating onto a conductive substrate using an electric current. ED coating is similar to CED (cathodic electrodeposition) coating, and the terms are often used interchangeably. This efficiency minimizes waste generation and optimizes material usage. It also reduces the amount of unused coating that requires disposal, leading to cost savings and environmental benefits. Coating processes typically operate at lower temperatures compared to other coating methods. The lower curing temperatures not only save energy but also reduce greenhouse gas emissions associated with energy production. Additionally, the ability to coat complex shapes and penetrate recessed areas reduces the need for multiple coating applications, further saving energy and resources.
Purpose of CED coating
- The purpose of CED coating is to provide a protective and decorative finish to various surfaces. It is a water-based coating process that involves the deposition of a thin, uniform film onto the surface of an object through an electrochemical reaction.
- The coating material is dispersed in a water-based solution and attracted to the surface being coated using an electrical charge.
- The primary purpose of CED coating services is to provide corrosion protection to the coated surface. The electrochemical process ensures that the coating material uniformly covers the entire surface, including hard-to-reach areas and recessed parts, providing excellent coverage and protection against rust and corrosion.
- CED coatings are known for their durability and resistance to environmental factors, making them suitable for various applications, including automotive parts, appliances, metal furniture, and other metal products.
- In addition to corrosion resistance, CED coatings also offer aesthetic benefits. The process allows for the application of a smooth, even, and consistent coating that enhances the appearance of the object.
- The coating can be customized to achieve different colours, gloss levels, and finishes, providing a decorative aspect to the coated surface.
Applications of CED coating
- Automotive Industry: CED coatings are extensively used in the automotive industry to protect various components from corrosion. This includes car bodies, chassis, engine parts, suspension systems, brake components, and other metal parts. CED coatings provide a uniform and durable protective layer that withstands harsh environmental conditions, contributing to the longevity and appearance of automotive products.
- Appliances and Electronics: CED coatings are applied to appliances such as refrigerators, washing machines, dishwashers, and air conditioning units to provide corrosion resistance and an attractive finish. In the electronics sector, coatings are used for coating electrical enclosures, connectors, and other metal components.
- Furniture and Decorative Items: used in the furniture industry to protect metal furniture, outdoor structures, and decorative items from corrosion. The coatings provide durability and a visually appealing finish to enhance the aesthetics of furniture pieces.
- Agricultural and Construction Equipment: applied to agricultural machinery, construction equipment, and heavy-duty vehicles to protect them from corrosion caused by exposure to outdoor elements and harsh operating conditions. The coatings ensure the longevity and reliability of this equipment.
- Industrial Applications: Find applications in various industrial sectors, including manufacturing equipment, machinery, metal structures, and infrastructure components. The coatings provide corrosion protection and extend the lifespan of these assets.
- Architectural Applications: CED coatings are used in architectural applications, such as coating metal doors, window frames, railings, and other building components. The coatings offer both protection and aesthetics, enhancing the appearance and durability of architectural elements.
- General Metal Coating: It can be used for general metal coating applications where corrosion resistance and a uniform finish are required.
Chemicals are commonly used in CED coating
- Resins: Resins play a crucial role in the CED coating formulation. They provide film-forming properties and adhesion to the substrate. Epoxy-based resins are commonly used in coatings for their excellent corrosion resistance and durability.
- Crosslinkers: Crosslinkers are chemical agents that promote the curing and crosslinking of the coating film. They enhance the mechanical and chemical properties of the coating, improving its resistance to abrasion, chemicals, and UV degradation.
- Pigments: Pigments are used to provide colour and opacity to the coating. Inorganic pigments such as titanium dioxide and iron oxide are commonly used for their stability and colourfastness.
- Conductive Additives: Since CED coating relies on an electrochemical process, conductive additives are included in the coating formulation to enhance the conductivity of the bath. These additives facilitate the uniform deposition of the coating material onto the substrate.
- Solvents: Water is the primary solvent used in coatings since it is an environmentally friendly and readily available option. However, small amounts of co-solvents may be used to adjust the viscosity and improve the flow characteristics of the coating solution.
Reducing the Environmental Footprint with CED Coating
- Minimizing Volatile Organic Compounds (VOCs): They are water-based, which means they contain lower levels of volatile organic compounds compared to solvent-based coatings. VOCs contribute to air pollution and can have harmful effects on human health. By using CED coatings, industries can reduce VOC emissions and improve air quality.
- Waste Reduction: They are designed for high transfer efficiency, ensuring that a significant portion of the coating material is deposited onto the surface being coated. This efficiency minimizes waste generation and optimizes material usage. It also reduces the amount of unused coating that needs to be disposed of, resulting in cost savings and a reduced environmental impact.
- Water conservation often incorporates closed-loop systems that capture and recycle excess coating material. This not only minimizes waste but also conserves water resources. Advanced filtration techniques enable the continuous reuse of the coating solution, reducing water consumption and the need for fresh water supplies.
- Energy Efficiency: CED coating typically operates at lower curing temperatures compared to other coating methods. The lower temperatures save energy and reduce greenhouse gas emissions associated with energy production.
- Compliance with Environmental Regulations: Processes typically comply with strict environmental regulations and standards regarding emissions, waste management, and worker safety.
Preserving the Planet through Sustainable Coating Practises
Cathodic electrodeposition coating offers significant environmental benefits as an eco-friendly surface finishing solution. By reducing VOC emissions, minimising waste generation, conserving water resources, and promoting durability, we contribute to sustainable practises and help protect the environment. Adopting ced coating as a preferred surface finishing method supports the goal of achieving a greener and more sustainable future for industries worldwide. Coating processes typically comply with strict environmental regulations and standards regarding emissions, waste management, and worker safety. Choosing CED coating solutions ensures compliance with these regulations and promotes responsible environmental stewardship. It provides excellent corrosion resistance and durability, extending the lifespan of coated products. This longevity reduces the need for frequent recoating or replacement, resulting in resource conservation and reduced waste generation.