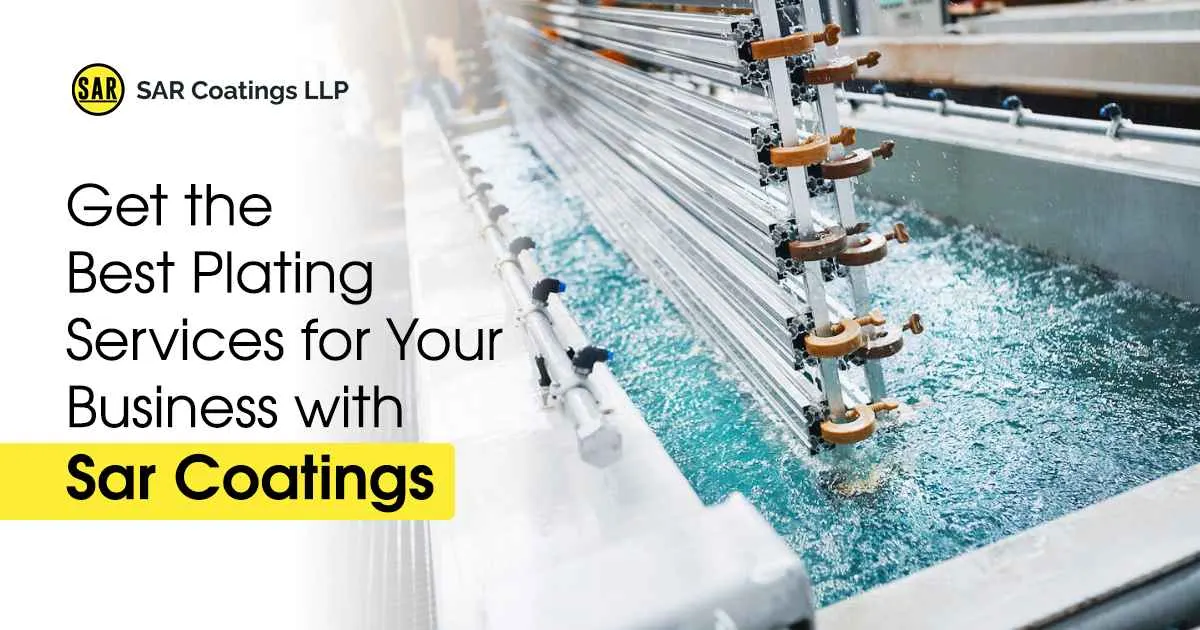
Get the best plating services for your business with Sar Coatings
Sar Coatings offers the best electroplating services for businesses, providing a range of high-quality coating solutions to meet your specific needs. Expertise and experience: Sar Coatings has a team of experienced professionals who specialize in plating services. They possess the knowledge and skills to handle various plating processes, ensuring excellent results for your business. Sar Coatings understands that different businesses have unique requirements. They offer customized plating solutions tailored to your specific industry, application, and desired outcomes. This ensures that you receive the most effective and suitable coating for your business needs.
It provides a wide range of plating options, including but not limited to electroplating, electroless plating, and various types of metal coatings. They can accommodate different materials, substrates, and finishes to meet your specific requirements. It maintains stringent quality control measures to deliver consistent and high-quality plating services. They utilize advanced equipment, industry-approved processes, and thorough inspection methods to ensure that the coatings meet or exceed industry standards. It understands the importance of timely delivery for businesses. They strive to provide efficient turnaround times, allowing you to meet your production schedules and deadlines without delays.
What are the four basic types of plating?
- Electroplating: Electroplating is the most widely used plating technique. It involves depositing a metal coating onto a substrate using an electric current. The substrate is the cathode (negative electrode), and a metal anode (positive electrode) is immersed in an electrolyte solution containing metal ions. When the current passes through the electrolyte, metal ions are reduced and form a thin layer on the substrate. Electroplating is used to enhance corrosion resistance, improve appearance, provide conductivity, and achieve specific surface properties.
- Electroless Plating: Electroless plating, also known as autocatalytic plating, does not require an external electric current. Instead, it utilizes a chemical reaction between the substrate and a plating solution to deposit a metal layer. The plating solution contains reducing agents that initiate the deposition process. Electroless plating provides uniform coatings and is often used for complex shapes, non-conductive surfaces, or materials that cannot withstand the electrical current required in electroplating.
- Immersion Plating: Immersion plating, also called displacement plating, involves immersing the substrate in a plating solution containing metal ions. Unlike electroplating, no external current is applied. Immersion plating is typically used for thin coatings, providing limited control over thickness and appearance.
- Electrochemical Plating: Electrochemical plating refers to a group of plating techniques that involve both electroplating and electroless plating processes. These techniques utilize electrochemical reactions to deposit metal layers on the substrate. Examples include electrochemical deposition (ECD), electrochemical displacement deposition (ECDD), and pulse plating. Electrochemical plating allows for precise control over coating thickness, composition, and surface properties.
What is a plating service?
A plating service refers to a process in which a thin layer of metal or other materials is applied to the surface of an object. This is done to enhance the appearance, provide protection, improve conductivity, or modify the surface properties of the object. The electroplating service process typically involves immersing the object, known as the substrate, in a solution containing metal ions or other coating materials. The plating service provider performs various steps to ensure proper adhesion and uniform coverage of the plating material on the substrate. These steps may include surface preparation, such as cleaning, polishing, or treating the substrate to remove impurities and promote bonding. The substrate is then carefully immersed in the plating bath or subjected to electroplating or electroless plating techniques. During the plating process, metal ions in the solution are attracted to the substrate's surface and form a layer that adheres to the substrate. The thickness of the plated layer can vary depending on the desired outcome and application requirements. Common metals used for plating include gold, silver, nickel, chromium, zinc, and copper, among others. Plating services find applications in various industries, including automotive, electronics, aerospace, jewellery, plumbing, and decorative items. The specific benefits of plating can include improved corrosion resistance, increased durability, enhanced aesthetics, improved conductivity, solderability, and wear resistance.
What are three examples of plating?
Three examples of plating commonly used in various industries are:
- Gold Plating: Gold plating involves depositing a thin layer of gold onto a substrate. It is commonly used in jewellery making, electronics, and decorative applications. Gold plating provides a lustrous, corrosion-resistant, and highly conductive coating. It is valued for its aesthetic appeal, durability, and ability to prevent tarnishing.
- Nickel Plating: Nickel plating, also known as nickel electroplating, is the process of depositing a layer of nickel onto a substrate. It is widely used in automotive, aerospace, electrical, and household applications. Nickel plating offers excellent corrosion resistance, wear resistance, and solderability. It can serve as a protective layer or a base for subsequent plating processes.
- Chrome Plating: Chrome plating, or chromium electroplating, involves depositing a layer of chromium onto a substrate. It is commonly used in automotive parts, plumbing fixtures, and various decorative applications. Chrome plating provides a bright, reflective, and corrosion-resistant coating. It enhances the appearance of the substrate, improves durability, and facilitates easy cleaning.
What specific properties and characteristics are you looking for in the coating?
- Corrosion Resistance: If the plated parts will be exposed to moisture, chemicals, or other corrosive environments, a coating with excellent corrosion resistance is essential to protect the underlying material.
- Wear Resistance: For parts that undergo friction or wear, a coating with high wear resistance can help extend their lifespan and improve durability.
- Electrical Conductivity: In applications where electrical conductivity is required, such as electronic components or connectors, a coating with good conductivity is necessary to ensure proper functioning.
- Aesthetics and Decorative Appeal: If the appearance of the plated parts is important for your business, consider coatings that offer a visually appealing finish, such as high reflectivity, smoothness, or specific colors.
- Adhesion and Bonding: The coating should have strong adhesion to the substrate material to ensure longevity and prevent peeling or delamination.
- Lubricity or Low Friction: For parts that require reduced friction or sliding properties, a coating with lubricious properties can be beneficial.
- Hardness and Abrasion Resistance: Certain applications may require a coating with high hardness and abrasion resistance to withstand mechanical stresses or abrasive environments.
- Thermal Stability: If the plated parts are exposed to high temperatures, a coating with good thermal stability is necessary to maintain their integrity and performance.
- Biocompatibility: In industries such as medical or pharmaceutical, where the plated parts will come into contact with the human body, biocompatible coatings are important to ensure compatibility and safety.
- Environmental Considerations: Depending on your business's sustainability goals, you may prioritize coatings that are environmentally friendly, free from hazardous materials, or comply with specific environmental regulations.
Will the plated parts require any additional treatments or finishing processes?
To enhance the surface smoothness and achieve a high-gloss finish, plated parts may undergo polishing or buffing processes. This helps remove any imperfections and create a visually appealing appearance. Passivation is a chemical process that removes any free iron or other contaminants from the surface of the plated parts, enhancing their corrosion resistance. It is commonly performed on stainless steel or other corrosion-resistant materials. Adding a topcoat or clear coating to plated parts can provide an extra layer of protection, improve durability, and enhance the aesthetic appeal of the surface. This can be particularly useful for decorative plating services. Proper cleaning and surface preparation are crucial before the plating process to ensure good adhesion and quality results. Depending on the substrate material and the presence of contaminants, specific cleaning methods such as degreasing, pickling, or abrasive cleaning may be required. Once the plating process is complete, quality inspection and testing may be performed to verify the coating's integrity, thickness, adhesion, and other relevant properties. This helps ensure that the plated parts meet the required standards and specifications.
Choose Sar Coatings for the best plating services and elevate your business's performance and quality
When it comes to getting the best plating services for your business, Sar Coatings is your ideal partner. With our expertise, commitment to quality, and comprehensive range of plating solutions, we ensure that your plated parts meet the highest standards of performance and durability. Our team of skilled professionals, state-of-the-art facilities, and adherence to industry best practices make us the trusted choice for businesses seeking top-notch plating services. Experience the difference with Sar Coatings and elevate your business's performance and quality. Contact us today to discuss your plating needs, and let us provide you with exceptional service that exceeds your expectations.