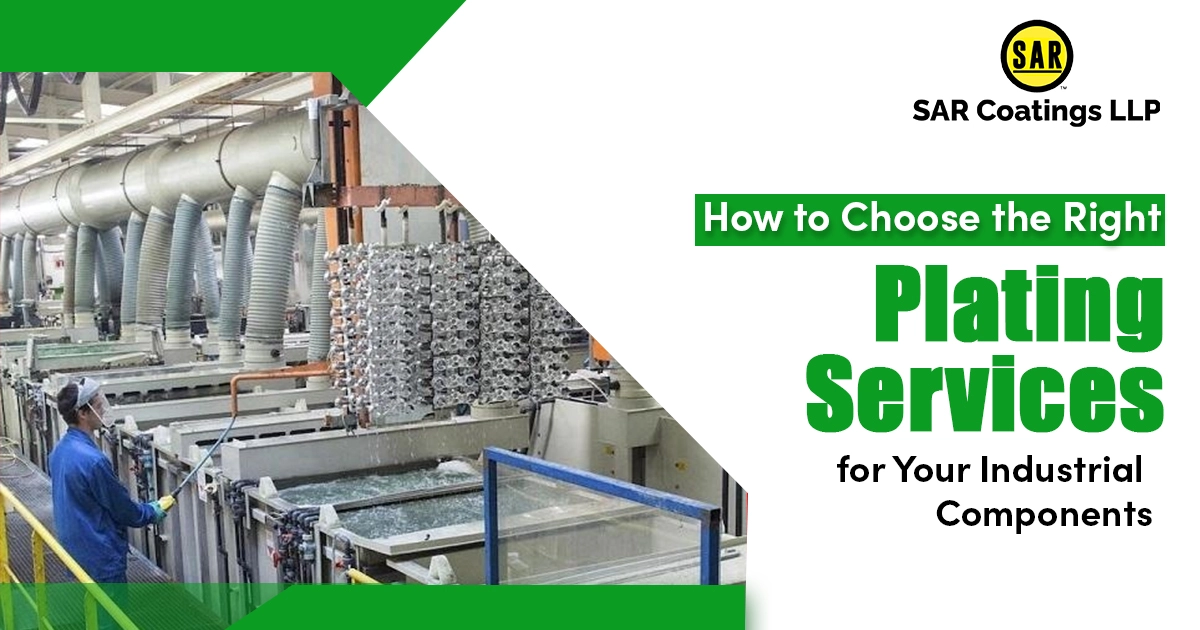
How to Choose the Right Plating Services for Your Industrial Components
Selecting the optimal plating service for your industrial components influences performance, lifespan, economic value, and conformity to regulatory standards; it is not just a matter of enhancing looks or introducing a finish that shines. Having an educated choice is paramount because there are a wide range of different plating processes and each is suitable for specific reasons and circumstances.
This article shall discuss the plating service, its relevance, and—and most importantly—how to analyze and choose the best service supplier for your own specific industrial needs.
What is Industrial Plating, and Why is it Important?
Applying a metal coating to a substrate—typically another metal—in order to obtain desirable characteristics like conductivity, corrosion resistance, wear resistance, or aesthetic appeal is known as industrial plating. Typical plating styles consist of:
- Excellent corrosion resistance, particularly in the automotive and aerospace industries, is a feature of zinc-nickel plating.
- High-performance fasteners frequently have zinc flake coating, which offers sacrificial protection.
- Parts with intricate geometries benefit greatly from the consistent coating provided by electroless nickel plating.
- A non-metallic substitute that offers both protection and aesthetic finishes is powder coating.
Depending on your application, environment, and financial constraints, each approach offers advantages and disadvantages.
Start by assessing the operational conditions of your component:
Key Factors to Consider When Choosing a Plating Service
1. Understand Your Application Requirements
- Will it be exposed to moisture, chemicals, or salt spray?
- Does it require electrical conductivity or insulation?
- Will the component experience mechanical wear or abrasion?
- Is appearance a priority, or is functionality the main concern?
Knowing definite performance targets makes it possible to determine the optimum coating type. For example, zinc-nickel plating is typically specified for applications that require maximum corrosion resistance and low to medium wear protection—such as under-hood auto components.
2. Material Compatibility
Not all plating operations can be used on all base materials. Aluminum, for instance, needs special surface preparation prior to plating, whereas steel and copper alloys can provide more ease of compatibility.
An experienced plating provider will analyze your component material and suggest processes that will guarantee good adhesion and consistent outcomes.
3. Industry Standards and Compliance
Plating operations tend to be regulated by trade guidelines—particularly in industries such as aerospace, defense, and medicine. Standards like ISO 9001, IATF 16949, or AS9100 indicate that the supplier is under strict quality measures.
Also, take environmental regulations into account. Does the supplier provide RoHS-compliant or hexavalent chrome-free solutions? Environmentally friendly alternatives such as trivalent chrome or zinc flake coatings are becoming more significant.
4. Quality Assurance and Testing
A reputable plating service should have robust quality assurance practices. Ask about their testing procedures:
- Salt spray testing for corrosion resistance
- Thickness measurement (X-ray fluorescence or micrometer)
- Adhesion and hardness testing
- Surface roughness and cleanliness verification
These tests ensure that your components meet both functional and aesthetic standards.
5. Customization and Flexibility
Your project might involve unique shapes, large parts, or high-volume batches. The right plating service should be able to:
- Handle your part size and geometry
- Offer both barrel and rack plating options
- Adjust thickness and finish to your specifications
- Scale production as needed—from prototypes to full production runs
Customization is key if you're working on high-precision components or specialized applications.
6. Lead Time and Turnaround
Where time-to-market is critical, lead time can be a show-stopper. See how quickly the supplier processes orders, particularly large ones or those requiring special finishes.
Also, keep in mind their logistics capacity—are they able to pick up and deliver? Do they have just-in-time (JIT) capabilities or make emergency turnaround available?
7. Cost vs. Long-Term Value
It’s tempting to go with the lowest quote, but cost shouldn't be the only factor. Consider:
- Durability: A more expensive plating might significantly extend component life.
- Performance: Will the coating reduce maintenance or improve product performance?
- Failure Risks: A subpar coating could lead to product failure, recalls, or increased warranty claims.
Look at the total cost of ownership rather than just the up-front price.
8. Reputation and Experience
Lastly, do your research. A proven plating supplier in your line of business is more likely to appreciate your difficulties and provide a well-suited solution.
Verify reviews, case studies or request client references. Duration of the company in business, return clients, and the capacity to manage large projects are also positive indicators of a good partner.
Final Thoughts
Selecting the proper plating service for your industrial parts is more than simply selecting a process—it's about finding a partner that knows your business, satisfies your technical needs, and provides consistent quality.
By carefully assessing your requirements, posing the right questions, and taking into account the long-term worth of the service, you can be sure that your components function reliably in their intended conditions—and that your investment in surface protection is worthwhile.
Regardless of automotive, aerospace, manufacturing, or heavy industry, the appropriate plating service has the potential to make a very big difference in product performance and cost of life.