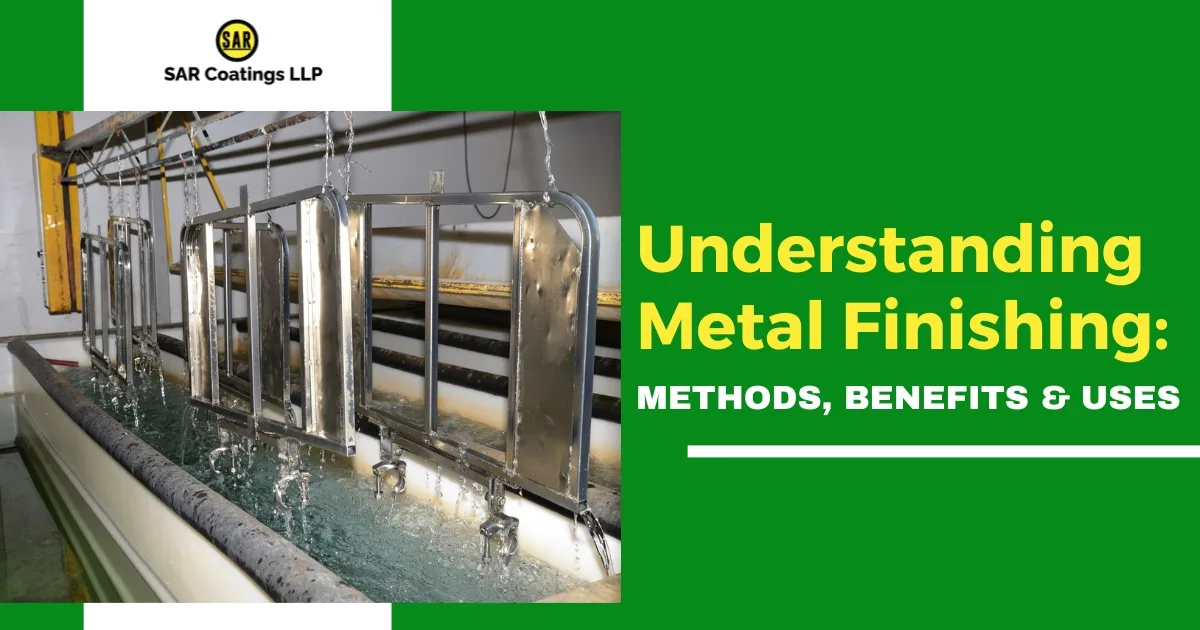
Understanding Metal Finishing: Methods, Benefits & Uses
Metal finishing is very essential in adding strength, utility, and look to metal goods. Various techniques for surface finishing include ED coating, plating, and painting surface treatment assist in performance improvement and life addition. The study explores different ways of metal finishing, their merits, and diversified applications.
Types of Metal Finishing
1. ED Coating: Electrodeposition Coating
ED Coating is a method of applying a protective paint layer using an electrical current. The technique provides uniform coverage, excellent adhesion, and corrosion resistance, making it widely used in the automotive, industrial, and marine sectors.
2. Plating
Plating is the process of depositing a metal layer on a substrate to enhance its properties. Common types include:
Electroplating: The process that uses electricity to deposit a uniform thin metal coating, like chrome, gold, or silver for aesthetic and protective purposes.
Electroless Plating: A chemical process without electricity to provide an even metal coating that enhances the performance by improving resistance to wear and tear.
3. Surface Treatment Painting
Surface treatment painting is basically comprised of powder coating and liquid painting services, which provide protective as well as decorative finishes. It increases the corrosion, chemical, and wear resistances.
Advantages of Metal Finishing
- Corrosion Protection: It prevents rusting and environmental deterioration.
- Durability Enhancement: It strengthens the metal parts and lengthens their lifespan.
- Aesthetic Enhancements: It offers several finishes and hues to enhance its appearance.
- Performance Improvement: It decreases friction, increases electrical conductivity, and promotes paint bonding.
Metal Finishing Applications
- Metal finishing has numerous applications. These include the following:
- Automotive: ED coating and plating protect parts of the vehicle from corrosion and wear.
- Aerospace: Surface treatment painting makes aircraft parts more durable.
- Electronics: Plating enhances conductivity and inhibits oxidation in printed circuits.
- Equipment Industrial: Powder and liquid painting services protect from harsh environmental conditions.
In-Depth Detail about Methods of Metal Finishing
ED Coating: An Explanation
ED coating, or electrodeposition coating, is a widely applied technique for applying a protective layer of paint or coating on metal surfaces. This process uses an electrolytically charged bath in which the metal component is submerged for an even coating application. The primary benefits of ED coating are superior corrosion resistance, smooth finish, and excellent adhesion properties. Automotive and industrial manufacturing rely on ED coating to extend the life of metal components.
Plating Techniques for Enhanced Protection
Another critical metal finishing process is the plating application, which makes a thin film of metal cover a base material to improve on its properties. Electroplating is one widely used plating technique for deposition of metals in gold, silver, copper, or nickel coatings on a substrate. The outcomes are an improved electrical conductivity of the metal plus wear resistance with protection against corrosion. Another variation, electroless plating, does not employ electricity but rather chemical reactions to form a uniform coating. This technique is especially useful for intricate parts that need uniform coverage.
Importance of Surface Treatment Painting
Surface treatment painting, which includes powder coating and liquid painting, offers aesthetic and protective benefits. Powder coating entails the electrostatic application of a dry powder that is then cured under heat. This process offers an extremely hard and rugged finish that does not chip and is also corrosion resistant. Liquid painting services use the solvent-based paints or water-based paints to achieve a smooth finish with quality. This method is applied when the application needs a thin layer or some color difference.
Why Metal Finishing Matters
Importance to metal finishing cannot be overlooked. Untreated metals tend to corrode, wear out, and lose surface integrity. The result will be loss of performance and eventual failure. In the use of proper metal finishing techniques, manufacturers can ensure that their products retain structural integrity, aesthetics, and functionality. This also promotes sustainability because it saves on frequent replacement and waste reduction.
Conclusion
An important part in manufacturing and maintenance processes is metal finishing, which yields added benefits of enhancement to durability, looks, and performance. In fact, ED coating, plating, and surface treatment painting are a must for protecting metal components in various industries. So, the investment of good quality time in metal finishing assures durability and reliability and is a part of the modern industrial practices.