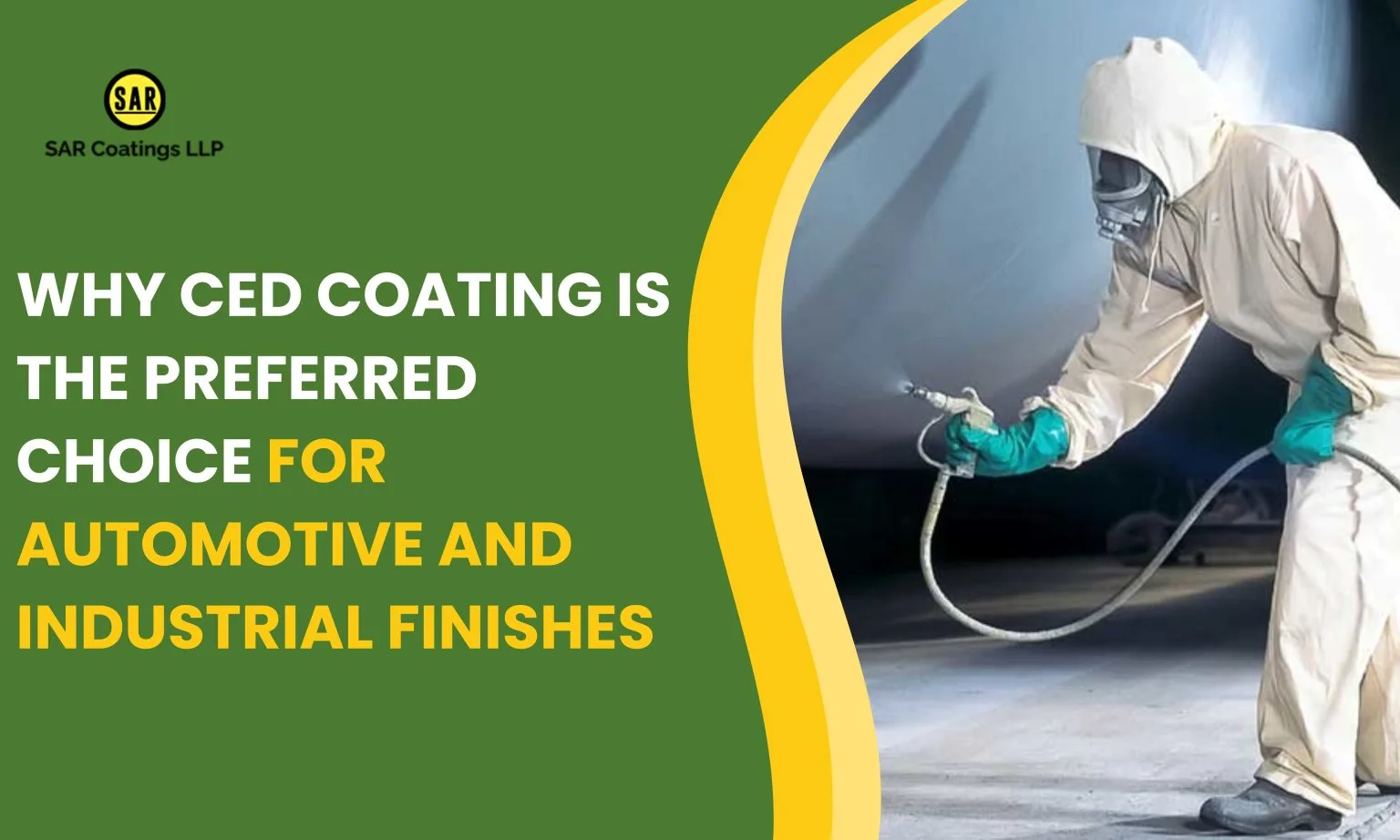
Why CED Coating is the Preferred Choice for Automotive and Industrial Finishes
In today’s fast-paced industries, ensuring the longevity and durability of components is more important than ever. CED coating, or Cathodic Electrodeposition Coating, has emerged as a leading solution in both the automotive and industrial sectors. Known for its superior resistance to corrosion, chemicals, and wear, CED coating has quickly become a preferred choice for protective finishes. Let’s dive into the details.
How Does CED Coating Work?
The CED process relies on electrophoresis, where electrically charged particles are deposited onto a surface using a cathodic electric current. Here’s a step-by-step explanation of how it works:
- Surface Preparation:
- The metal surface is thoroughly cleaned to remove dirt, grease, and impurities.
- Pre-treatment includes phosphate coating to improve adhesion.
- Electrocoating:
- The metal component is submerged in a water-based coating solution.
- An electric current is applied, causing the paint particles to migrate and adhere to the surface.
- Deposition:
- The coating material evenly spreads across the surface of the substrate.
- The thickness of the coating is precisely regulated by modifying the electric current.
- Curing:
- The coated component is baked at high temperatures to harden and cure the finish.
- This process creates a smooth, durable, and corrosion-resistant layer.
The use of an electric current ensures that every surface, including hidden and intricate parts, is evenly coated. Businesses seeking CED Coating services in Gurgaon can benefit from this advanced process, which ensures precision and consistency unmatched by other coating techniques.
Benefits of CED Coating
CED coating offers numerous advantages that make it superior to traditional coating methods.
- Superior Corrosion Resistance:
CED coatings provide unmatched protection against rust and corrosion, making them ideal for components exposed to moisture, chemicals, and harsh environments. - Uniform Thickness and Coverage:
Unlike spray painting or powder coating, the CED process ensures an even coating thickness, even on complex and hard-to-reach surfaces. - Cost-Effectiveness:
The process reduces wastage of materials and requires less manual labor, resulting in significant cost savings. - Durability and Longevity:
CED-coated components are highly durable and offer a longer lifespan, reducing maintenance costs. - Eco-Friendly:
Water-based CED coatings have low VOC (volatile organic compound) emissions, making them environmentally sustainable.
For companies in industrial hubs like Manesar, opting for CED Coating services in Manesar ensures a durable, eco-friendly, and cost-efficient solution.
Why CED Coating is Preferred in the Automotive Industry
Automotive manufacturers rely heavily on CED coating to protect critical components. Here’s why it is the preferred choice:
- Protection of Automotive Components:
CED coating provides a tough barrier against rust, road salt, and chemicals, ensuring that vehicle components like chassis, panels, and underbody parts remain corrosion-free for years. - Resistance to Environmental Factors:
Vehicles face constant exposure to moisture, temperature variations, and corrosive substances. CED coating ensures components withstand these challenges. - Enhanced Aesthetic and Quality:
The smooth, uniform coating improves the appearance of vehicle parts, ensuring a high-quality finish that meets industry standards.
Leading automakers integrate CED coating into their assembly lines for everything from body panels to nuts and bolts, highlighting its versatility and reliability.
Also Read: How CED Coatings Support Sustainability Goals in 2025
Why CED Coating is Preferred in Industrial Finishes
In industrial settings, components and machinery are subjected to extreme conditions, from chemical exposure to heavy wear and tear. CED coating addresses these challenges effectively:
- Durability Under Harsh Conditions:
Industrial tools, equipment, and parts often operate in harsh environments. CED coatings ensure they remain rust-free and functional for longer periods. - Improved Component Lifespan:
The durability of CED-coated components reduces the need for frequent replacements and maintenance, leading to cost savings. - Versatility in Applications:
CED coating is used on a variety of industrial equipment, from agricultural machinery to electrical components and heavy-duty tools.
For industries aiming to reduce downtime and enhance productivity, CED coating is a game-changer.
Comparison Between CED Coating and Other Coating Methods
CED coating outshines other methods due to its unique properties. Let’s compare it with a few alternatives:
- CED Coating vs Powder Coating:
- Powder coating is thicker but lacks the ability to cover hidden areas.
- CED provides better uniformity and reaches intricate surfaces effectively.
- CED Coating vs Spray Painting:
- Spray painting results in uneven finishes and higher wastage.
- CED offers precision, efficiency, and minimal material loss.
- CED Coating vs Galvanization:
- Galvanization offers corrosion resistance but adds significant weight.
- CED coating achieves corrosion resistance without additional bulk.
Conclusion
CED coating has revolutionized the way automotive and industrial components are protected and finished. Its superior corrosion resistance, durability, cost-effectiveness, and eco-friendly attributes make it the preferred choice across industries. By combining advanced technology with practical benefits, CED coating ensures that components perform reliably, even in the harshest conditions. As industries evolve and embrace sustainability, CED coating will continue to play a crucial role in delivering high-quality finishes and long-lasting performance.